Статьи и публикации
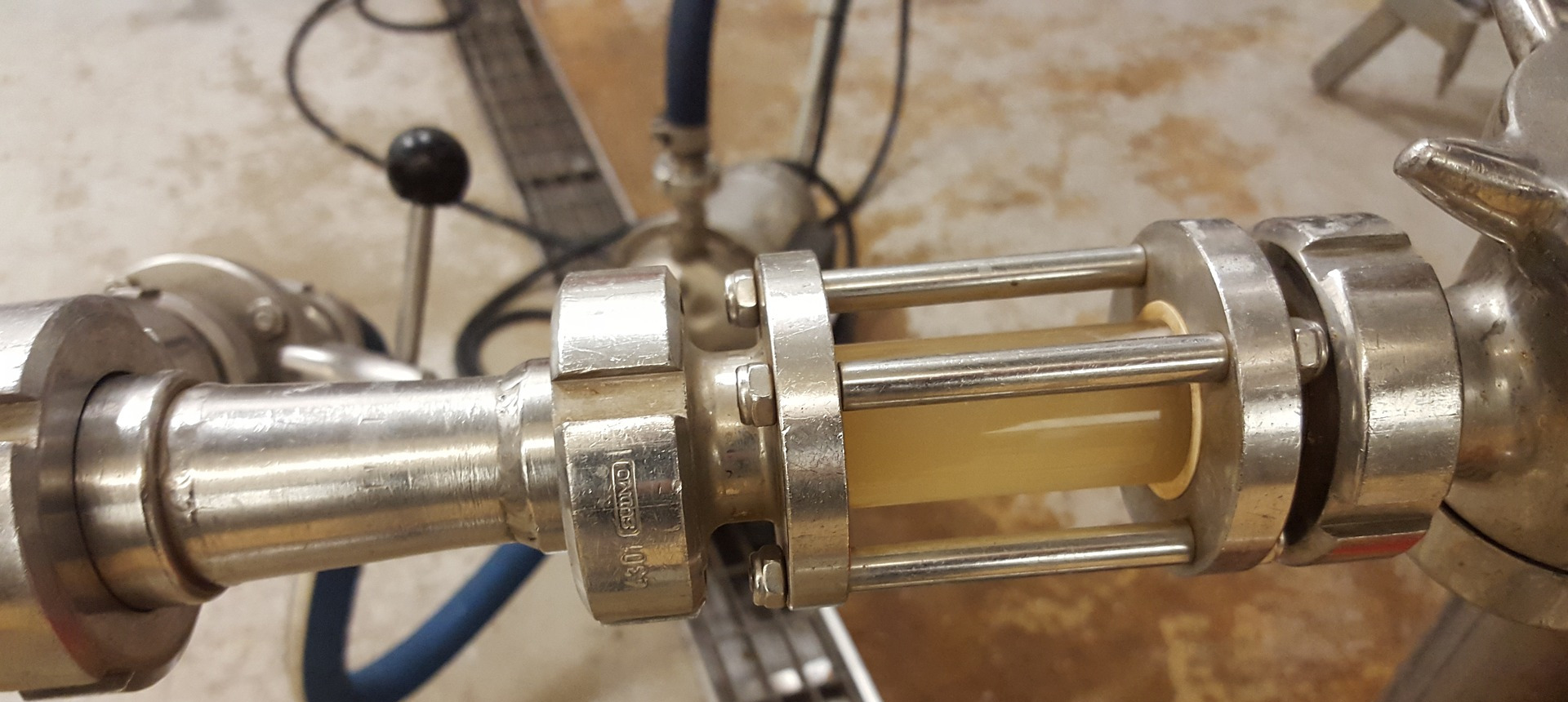
Основы фильтрации
Как правило, небольшие заводы выпускают нефильтрованное пиво, то есть оно поступает на розлив сразу после дображивания, например из ЦКТ, или отправляется потребителю, а дображивание и созревание происходят в бутылке или в бочке. При этом оно может быть хорошо осветленным, но не иметь блеска из-за наличия в нем во взвешенном состоянии дрожжей, белков, полифенолов. Для удаления этих и других веществ и частичек в целях получения прозрачного с блеском готового напитка или просто для увеличения ассортимента пиво фильтруют. В настоящей статье рассмотрены главные составляющие процесса фильтрации, а также факторы, обусловливающие ее качество.
Оборудование и материалы для фильтрации
Правильный выбор фильтрующего оборудования имеет решающее значение для достиженья желаемого результата при минимальных затратах. Существует большое разнообразие оборудования: от относительно небольших фильтров до фильтрационных систем как прямого потока (иногда эти системы называют тупиковыми), так и поперечного потока (системы тангенциальной фильтрации). Доступно множество фильтрующих материалов, различающихся своей конструкцией, рабочими характеристиками, механизмами разделения. Часто руководителю, инженеру-технологу бывает очень сложно сделать правильный выбор. Предлагаю начать наш разговор со вспомогательных материалов, которые используются при производстве пива. Основной фильтрацией до сих пор остается относительно грубая намывная фильтрация. Для нее используют такие вспомогательные фильтрующие материалы, как кизельгур, перлит, целлюлоза. Кизельгур — это диатомитовая земля, образованная ископаемыми одноклеточными инфузорными водорослями. Благодаря происхождению этот материал имеет большой объем пор и хорошую адсорбирующую способность. С месторождений кизельгур поступает на обработку, которую проводят тремя способами. Первый из них — это сушка: кизельгур сушат при температуре 400 °C, сохраняя естественную форму оболочки и пористость. Этим способом получают «тонкий» кизельгур. Второй способ — это прокаливание, в результате которого получают кизельгур, называемый кальцинированным. Высушенный кизельгур нагревают до 800 °C, при этом внешние слои спекаются, образуя более крупные частицы, а внутренняя пористая структура остается без изменений. Третьим способом получают «грубый» кизельгур. К сырому материалу добавляют хлорид или карбонат натрия и затем нагревают до 800- 900 °C (температура плавления диоксида кремния), в результате чего образуются крупные конгломераты. Кизельгур является основным фильтрующим материалом из-за своей высокой пористости. Его удельная поверхность может доходить до 20-40 м2/г. Кроме того, важной характеристикой, влияющей на экономичность фильтрации, является его плотность во влажном состоянии. Чем выше ее значение, тем больше расход кизельгура и больше прирост давления при постоянном осветляющем эффекте и производи тельности. В табл. 1 приведены средние показатели для кизельгура основных фракций, применяемых при фильтрации пива. При фильтрации грубую фракцию используют для создания опорного слоя на поверхности горизонтальных сит, свечей, картона или картриджей, а более мелкие фракции создают глубинный фильтрующий слой. Также кизельгур нашел свое место в производстве фильтр-картона и фильтрующих моду лей - он входит в их состав. Но, к сожалению, кизельгур - очень дорогой фильтрующий материал. После фильтрации 1 гл пива остается до 500 г кизельгурового шлама; для количественной наглядности: после фильтрации 10 тыс. гл пива - около 5 тыс. л. Утилизация шлама в виде «бытовых отходов» запрещена. Пивоваренное производство вынуждено искать варианты утилизации кизельгура, в качестве которых могут быть, например, такие, как захоронение на специальных полигонах или применение в виде удобрения на полях, а также дополнительного материала при производстве кирпича, асфальта и бетона. Термическая регенерация кизельгура для повторного применения - достаточно дорогой и трудоемкий процесс.
Средние показатели для кизельгура основных фракций, применяемых при фильтрации пива
Показатель | Кизельгур | ||
некальцинированный (тонкая фракция) | кальцинированный (средняя фракция) | кальцинированный с флюсом (грубая фракция) | |
Удельная поверхность, м2/г | 12-40 | 2-5 | 1-3 |
Плотность во влажном состоянии, г/л | 270-380 | 280-400 | 300-500 |
Проницаемость, Д* | 0,08-0,15 | 0,15-0,30 | 0,9-2,0 |
* Д (дарси) - внесистемная единица проницаемости пористых сред, приближённо равная 1 мкм2.
Другой минеральный вспомогательный материал, который также иногда используют для фильтрации, - перлит. Это материал вулканического происхождения - силикат алюминия (Al2O3*SiO2). Перлит нагревают до 800 °C, содержащаяся в нем влага расширяется и приводит к вспучиванию и растрескиванию. Далее полученную стекловидную структуру измельчают до необходимых размеров в зависимости от фракции. При значениях pH готового пива (4,5) из перлита выделяются железо и известь, что может негативно сказаться на конечном продукте. В связи с этим для фильтрации пива перлит в наши дни практически не применяется.
Подводя итог, к общим недостаткам при использовании минеральных фильтрующих материалов можно отнести:
- необходимость утилизации;
- опасность для здоровья операторов (кристаллический кремний при вдыхании может быть вреден для здоровья, его особенно много в грубых сортах кизельгура);
- вероятность вымывания нежелательных ионов, способствующих окислению пива;
- износ фильтрующего оборудования из-за абразивности кремния;
- неравномерность гранулометрического состава, из-за чего нередко грубый кизельгур тяжело поднимается на верхние элементы горизонтального и свечного фильтров, из мелких частиц образуется слабый кизельгуровый слой, который пропускает частицы кизельгура, дрожжевые клетки в фильтрат.
В связи с этим в настоящее время все большую популярность получают фильтрующие материалы растительного происхождения, которые не имеют недостатков кизельгура и перлита. В последнее время целлюлозу все чаще рассматривают как вспомогательное или основное средство для намывной фильтрации. При использовании целлюлозы фильтрующий слой не растрескивается, устойчив к перепаду давлений, закрывает небольшие дефекты сетки фильтра, легко удаляется благодаря своей стабильности. При равной производительности обеспечивается более высокая удерживающая способность и более долгий цикл фильтрации. Несмотря на более высокую цену целлюлозы за единицу продукции, общая себестоимость фильтрации с применением этого материала может быть аналогична кизельгуровой при значительно более высоком качестве фильтрата. Целлюлозу можно использовать как только для первого намыва, заменяя грубый кизельгур (примерно в том же количестве 500 г/м2), так и для всего цикла фильтрации. Рецептуры намыва и дозации подбирают индивидуально. Длинноволокнистую целлюлозу применяют для предварительного слоя, а целлюлозное волокно средней длины и короткие волокна целлюлозы - для осветляющей и тонкой фильтрации. Мы рассмотрели вспомогательные материалы, но их использование без основного фильтрационного оборудования невозможно.
Намывные фильтры и намывная фильтрация
Виды намывных фильтров
Фильтрация пива, как правило, - ступенчатый, каскадный процесс. Вначале пиво фильтруется с помощью кизельгура, целлюлозы на намывных фильтрах. Для этого используют следующие их виды:
- рамные (фильтр-пресс);
- емкостные:
- вертикальные, свечные (с металлическими или полипропиленовыми фильтрующими элементами в виде свечи),
- горизонтальные (с фильтрующими элементами в виде тарелок).
В намывных фильтрах есть опора, на которую и осуществляется намыв. В рамном фильтр-прессе ею служит опорный регенерируемый фильтр- картон, в горизонтальном емкостном фильтре - сито из нержавеющей стали, размер пор которого равен 55-80 мкм. В свечных фильтрах размер пор металлического фильтрующего элемента составляет 50-100 мкм, а полипропиленовой свечи-картриджа - 0,5-5,0 мкм.
Принцип намывной фильтрации
Поры фильтр-картона, сит, свечей часто большего размера, чем у кизельгура, поэтому при намыве суспензия кизельгура и/или целлюлозы циркулирует при постоянной скорости потока (в 1,5 раза выше скорости фильтрации) и избыточном давлении не менее 2 бар до тех пор, пока не выстроится стабильная матрица. Частички кизельгура опираются друг на друга и взаимно препятствуют своему дальнейшему продвижению. Удерживание крупных и связывание мелких частиц приводит к образованию фильтрующего слоя и получению прозрачного фильтрата. Процесс намыва слоев занимает примерно 10-15 мин. Рецепт намыва кизельгура получают путем индивидуального подбора в зависимости от пива и оборудования. Во время намыва и фильтрации важно не допускать завоздушивания фильтра. В течение цикла фильтрации необходимо дозировать кизельгур (текущая дозировка 60- 120 г/гл) для сохранения проницаемости фильтрующего слоя и, следовательно, поддержания постоянной производительности, то есть прироста разности давлений (вход/выход), который должен медленно и равномерно возрастать (у рамных фильтров - 0,2-0,3 бар/ч, у емкостных - до 0,5 бар/ч) до предельного максимального избыточного давления. При использовании силикагелей (вспомогательный материал для стабилизации пива) количество тонкого кизельгура в текущей дозировке может быть соответственно сокращено.
Описание фильтрующих установок
Теперь коротко о самом оборудовании. В любую фильтрующую намывную установку входит емкость для приготовления суспензии кизельгура, дозатор, насосы. Намывной рамный фильтрпресс состоит из станины, на которую поочередно установлены пластины и рамы для осадка. На пластины навешивается фильтр-картон. Во время фильтрации этот фильтр-пакет сжимается. Кизельгур во время намыва и текущей дозировки поступает в рамы, а отфильтрованное пиво выходит через пластины. Пластины фильтра для фильтрации пива должны быть выполнены из нержавеющей стали для обеспечения возможности качественной стерилизации с использованием высокой температуры. Также фильтр с пластинами из нержавеющей стали гарантирует более высокое максимальное давление (до 8 бар). Намывной свечной фильтр - цилиндрическая вертикальная емкость с коническим дном. В верхней части, под крышкой, находится перфорированная пластина, к которой подвешены фильтрующие свечи. В одном фильтре может быть до 700 свечей длиной свыше 2 м, что обеспечивает очень большую площадь фильтрации. Основной недостаток традиционных свечных фильтров - неравномерный намыв. Так как поток идет снизу вверх и упирается в перфорированную пластину, скорость замедляется и в верхней части свечи намывается больше мелких частиц. Намывной фильтр с горизонтальными ситами также представляет собой цилиндрическую вертикальную емкость. По центру размещен полый вал, на котором расположены круглые фильтрующие элементы - сита. Сам процесс намыва и фильтрации в принципе такой же, как и на свечном фильтре. И недостаток тот же - из- за большого объема возникает неконтролируемый поток, получается неравномерный намыв кизельгура. Чем дальше от вала, тем более толстый слой грубых частиц, а ближе к валу - более тонкий слой мелких частиц (рис. 1).
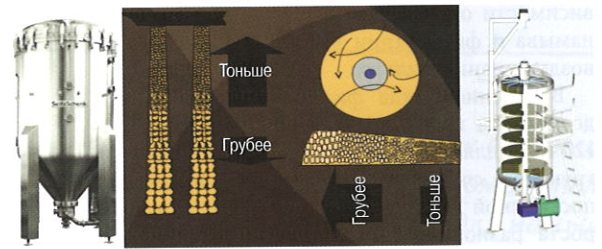
При фильтрации на традиционных емкостных фильтрах хорошим считается результат, если количество дрожжей в фильтрованном пиве не превышает 5 клеток в 100 мл фильтрата. В последнее время для заводов малой и средней мощности предлагают новый вид свечного намывного фильтра, в котором в качестве свечи применяют полипропиленовый картридж с рейтингом 0,5 мкм. При использовании данного оборудования за один шаг фильтрации пиво проходит две ступени: кизельгуровую намывную фильтрацию и трап-фильтрацию. Фильтрующая поверхность данного фильтра разделена на несколько емкостей (фильтродержателей) небольшого объема, благодаря чему фильтрующий материал распределяется по поверхности фильтрующего элемента максимально равномерно и обеспечивает качественный результат фильтрации в каждой точке фильтрующей поверхности. Кроме того, при применении полипропиленового картриджа с рейтингом 0,5-3,0 мкм можно отказаться от грубого кизельгура как наиболее вредного для здоровья человека и использовать только среднюю и тонкую фракции. На рис. 2 показан фильтр ASF, состоящий из базового модуля (ВМ7), промежуточных модулей (максимально возможно - три) (ZM7) и конечного модуля (ЕМ7). Наличие промежуточных модулей дает возможность изменять производительность путем подключения или отключения модулей. Ваше производство растет, и ваш фильтр тоже. В межсезонье можно уменьшить производительность. Плюсом по сравнению с рамным фильтром является то, что система закрыта, нет доступа кислорода, нет подкапывания, что лучше для микробиологии пива и санитарии самого производства. Недостатком этого типа фильтра является ограниченная мощность конструкции. Производительность выпускаемого фильтра составляет от 5 до 80 гл/ч. При планировании нового намывного фильтра важно предусмотреть возможность контроля следующих величин:
- разницы давления (наличие манометров в санитарном исполнении) на входе и выходе фильтра;
- скорости потока как при фильтрации, так и при намыве, мойке и стерилизации (наличие расходомера);
- мутности фильтрата.
Кроме того, должна существовать возможность проведения качественной мойки и стерилизации фильтра (доступность для промывки поверхностей как самого фильтра, так и дополнительного оборудования, в частности дозирующего насоса, клапанов, трубопроводов, и их устойчивость к воздействию высокой температуры и химических сред). Так как при намывной фильтрации возможен проскок как дрожжей, так и самого вспомогательного фильтрующего материала, в традиционной схеме фильтрации пива часто используется вторая ступень фильтрации. Для этого возможны следующие варианты фильтров:
- пластинчатый фильтр-пресс;
- модульный;
- картриджный;
- тангенциально-поточный (cross-flow).
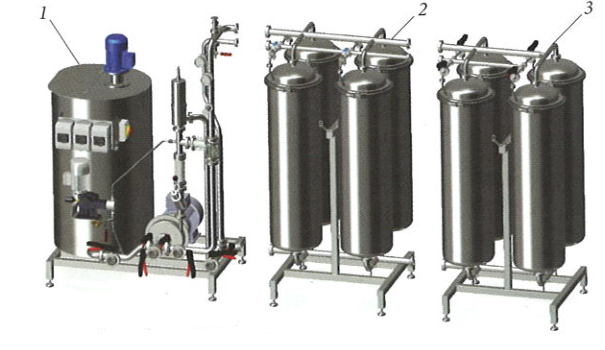
1 - базовый модуль; 2 - промежуточный модуль; 3 - конечный модуль
Фильтрующие элементы
При производстве напитков и, в частности, пива взвешенные частицы могут быть твердыми или мягкими, трудно и легко деформируемыми. Их распределение по размерам может быть однородным, находящимся в определенном интервале (например, 1-5 мкм), или гетерогенным, с широким распределением частиц по размерам (например, 0,5-500 мкм). Они варьируют от микронных до больших размеров в миллиметровом диапазоне и больше. Микрон составляет одну тысячную долю миллиметра, или одну миллионную долю метра. Мы можем невооруженным глазом видеть частицы, размер которых составляет более 40 мкм. Поэтому если для каких-то задач требование по качеству сводится исключительно к устранению видимых частиц, то достаточно установить фильтры с абсолютным рейтингом 20 мкм либо с номинальным рейтингом 5 мкм. И для этих целей мы можем выбрать фильтр-картон, картриджные или мешочные фильтры. Плоские листы фильтр-картона известны всем, они уже более 100 лет используются в пищевой промышленности. Уникальная матрица фильтрующего материала, состоящая из целлюлозы, диатомита и перлита, а также возможность совместить три механизма удержания: поверхностный, глубинный и адсорбционный делают фильтрацию на картоне привлекательным вариантом. Во многих случаях ее крайне трудно заменить другими технологиями из-за большой поверхности фильтрации и грязеемкости. Фильтр-картон устанавливают в пластинчатый фильтр-пресс. От намывного рамного фильтра он отличается отсутствием рам для осадка и состоит только из пластин, между которыми укладывается фильтр-картон. Традиционные рамные фильтры имеют существенные недостатки, такие как высокие издержки по замене и очистке фильтроэлементов, открытая система в сочетании с потерями продукта при подкапывании, риск микробиологического загрязнения и необходимость в существовании пространства для установки фильтра. С середины восьмидесятых годов листовой фильтр-картон начали выпускать в виде модулей. Представляют они собой индивидуальные ячейки, изготовленные из двух листов фильтр-картона, отделенные друг от друга внутренним и внешним полипропиленовыми сепараторами. Это исключает деформацию листов после тепловой обработки, обратной промывки и закупоривание ячеек из-за минимального расстояния между ними. Корпуса для установки модулей, так же как для картриджных и мешочных фильтров, представляют собой закрытую конструкцию (нет подкапывания, нет доступа кислорода), удобны и просты в обслуживании, занимают минимум площади. Но прогресс не стоит на месте, и недавно появилась новая конструкция модуля, в которой на проницаемый опорный сердечник намотан фильтр-картон с расположенными в его слоях каналами для исходного продукта и фильтрата. Один 16-дюймовый модуль эквивалентен 8-10 м2 листового фильтр-картона (это значит, что два модуля эквивалентны 100 листам фильтр-картона размером 40 х 40 см). Благодаря применению данной технологии укладки фильтрующего материала происходит лучшее осветление продукта и фильтр имеет большую грязеемкость. Конструкция корпуса позволяет вмещать от 1 до 6 модулей.
Особенности тангенциальнопоточной фильтрации
Вспомогательные материалы — это главный недостаток намывной фильтрации, поэтому в последнее время все более интересен альтернативный вариант фильтрации без кизельгура с использованием технологии тангенциально-поточной фильтрации. Поскольку эта технология пока еще достаточно дорога для заводов малой и средней мощности, в рамках этой статьи подробно останавливаться на ней мы не будем. Это самостоятельная большая тема, заслуживающая отдельной публикации. Если кратко, то при тангенциально-поточной фильтрации, или cross-flow-фильтрации, нефильтрованный продукт циркулирует вдоль фильтрующей поверхности (мембраны), а пермеат (фильтрат) проходит через нее. На ее поверхности при этом остаются частицы мути, которые после блокировки мембраны смываются обратным потоком. В зависимости от типа фильтрующей поверхности пиво на фильтрацию может подаваться после предварительной сепарации или без нее. Однако часто производители оборудования, не требующего предварительной сепарации, устанавливают ограничения по количеству дрожжевых клеток на входе в фильтр (рис. 3). Также при принятии решения использовать мембранный фильтр с сепаратором или без него необходимо тщательно продумать вопрос стабилизации пива, так как использование традиционных методов стабилизации, в частности с помощью силикагелей, усиливает нагрузку на мембрану, снижая производительность и экономичность фильтрации. К основным преимуществам использования тангенциально-поточной фильтрации через половолоконные мембраны можно отнести следующие:
- полная автоматизация процесса;
- отсутствие таких расходных материалов, как кизельгур, соответственно, не требуется место для его хранения и проведения прочих погрузочно-разгрузочных работ, связанных со вспомогательными материалами, отсутствует необходимость утилизации отработанного кизельгура;
- применение особого расходного материала - мембранного модуля, который меняется один раз в один-три года, в зависимости от количества циклов мойки и стерилизации;
- возможность применения на производствах с частой сменой сортов;
- повышение стабильности вкуса;
- снижение мутности (особенно механической) по сравнению с кизельгуровой фильтрацией;
- надежная редукция дрожжей и снижение бактериальной нагрузки;
- уменьшение потерь пива;
- снижение потребления воды, углекислоты и уменьшение количества твердых отходов.
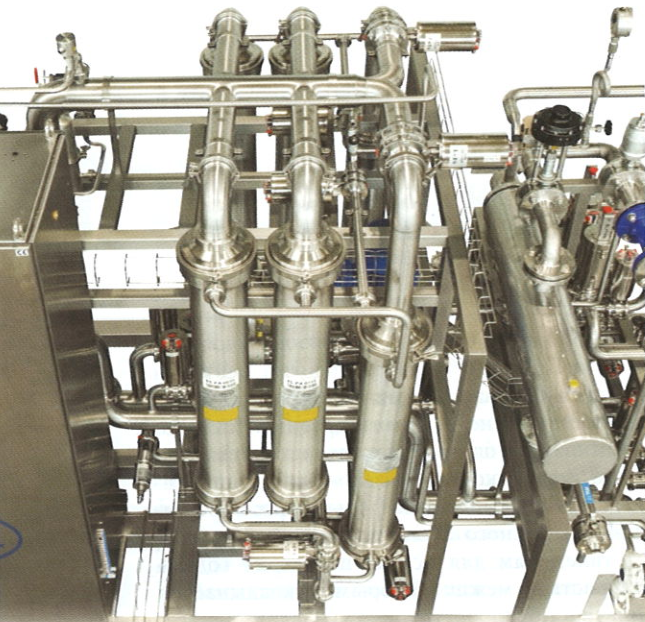
Мешочные и картриджные фильтры
Мешочные фильтры применяют только для удаления частиц и/или гелей. Эти фильтры в основном имеют номинальное удержание и хорошо подходят для грубой фильтрации и случаев, когда некритичен проскок нескольких частиц. Плюс при использовании мешков — это закрытый корпус, который занимает мало производственного места. Картриджные фильтры удаляют твердые частицы, гели, коллоиды и микроорганизмы. Очень хорошо подходят для предфильтрации, осветления и удаления опалесценции. На пивзаводах используются для фильтрации не только пива, но и воды, моющих растворов, газа, пара, воздуха, а также для защиты «более тонких» и мембранных фильтров. Есть картриджи, которые сокращают микробиологическую нагрузку, удаляя крупные микроорганизмы (например, дрожжи), и мембранные стерилизующие картриджи, которые удаляют и более мелкие микроорганизмы. Об этом применении и принципиальном различии поговорим чуть позже. Для начала давайте обсудим эффективность удаления частиц.
Эффективность удаления частиц
К нам часто обращаются с просьбой предоставить фильтр с определенным рейтингом, а не подобрать необходимый фильтр для решения той или иной задачи, например: «Мне нужен фильтр с рейтингом пять микрометров». При этом, как правило, не учитывается эффективность удержания. Откуда берется рейтинг (выраженный в микронах) и эффективность (выраженная в процентах)? Эти величины каждый производитель определяет сам, и хорошо, если это делается на основании лабораторных испытаний. К сожалению, нет определенного стандарта для всех. В связи с этим фильтр с рейтингом 5 мкм одного производителя не тождествен фильтру с рейтингом 5 мкм другого производителя. Производители могут проводить измерения, фильтруя различные, отличающиеся как по природе, так и по размеру, частицы, например частички суспензии кварцевого песка, стеклянные латексные шарики, гранулы полистирола. Естественно, эти частицы имеют мало общего с морфологией микроорганизмов, поэтому с использованием частичек определяют эффективность удержания только у механических фильтров. Следовательно, не каждый фильтр с рейтингом 0,2 мкм является мембранным фильтром, или, как их еще называют, стерильным, микробиологическим, и может служить для удаления микроорганизмов. Производитель провел оценку этого фильтра только частичками, пусть и конкретного размера, но не фильтрацией суспензии определенного вида микроорганизмов. Это другой тест. Кроме этого, лабораторные испытания эффективности удаления частиц различаются:
- Количеством проходов нефильтрата - при зацикливании схемы нефильтрат циркулирует, многократно проходя через фильтр. Из задержанных частичек на поверхности фильтра образуется дополнительный фильтрующий слой.
- Методами измерения - подсчет частиц проводится по их массе или по размерам.
- Чувствительностью оптических счетчиков.
Поэтому некорректно сравнивать фильтры, оцененные по разным методикам испытаний.
К примеру, есть тест OSU-A2 по стандарту ISO 4572 ANSI В/93/31-1973, во время проведения которого осуществляется один проход нефильтрата. Фильтрация происходит при постоянной скорости, определенной концентрации частиц и известном распределении их по размерам. Количество частиц до и после фильтра измеряется высокочувствительными оптическими счетчиками.
Наверное, вы сталкивались с такими определениями, как «номинальный» и «абсолютный» фильтры. Эти термины используют для обозначения фильтра на основании его эффективности удержания частиц. В свою очередь эффективность удержания частиц (в процентах), которая иногда выражается через коэффициент β, определяется по формуле . Пример. Фильтр, задерживающий 1000 частиц определенного размера, например 3 мкм и более, и позволяющий только одной частичке пройти через себя, имеет эффективность удаления 99,9% для частиц размером 3 мкм и более. Коэффициент р при этом показывает соотношение частиц до фильтра к количеству после: 1000/1 = 1000. Коэффициент β = 1000.
На рис. 4 приведены два фильтра с одним рейтингом 3 мкм, но с различными значениями коэффициента β, и мы видим разный результат фильтрации (количество частичек после фильтра). Это показывают и данные в табл. 2. Через пять фильтров с одинаковым рейтингом 3 мкм пропускали определенное количество частиц – 5000 – и измеряли количество частиц, прошедших через фильтр. При этом мы видим, что эффективность удержания для фильтра А и фильтра Е различается на 9,98%, а коэффициент β — в 500 раз, следовательно, фильтр Е в 500 раз лучше фильтра А.
Нет стандартного определения терминов «номинальный» и «абсолютный» фильтр. Некоторые производители фильтров могут указывать, что фильтр номинальный при эффективности удаления 99%, в то время как другие могут рассматривать эффективность удаления 98% как показатель абсолютного фильтра. Поэтому важно знать не только то, какой фильтр – номинальный или абсолютный – вам предлагают, но и значение эффективности удаления частиц (в процентах) или коэффициента β.
Правильным было бы «номинальными» называть фильтры с нефиксированной структурой пор, допускающей проскоки частиц при колебании давления, и с миграцией самого фильтрующего материала. К номинальным относятся фильтр-картон, засыпные колонны, мешочные фильтры, особенно с прошитым швом. С другой стороны, существуют номинальные фильтры с фиксированной структурой пор, у них отсутствует миграция фильтрующего материала. Примерами таких фильтров являются мешочные фильтры более высокого качества со сварными швами и глубинные полипропиленовые картриджи.
Термин «абсолютный» применяется для фильтров со стабильной структурой пор с постоянным эффектом удаления при фиксированном размере частиц, отсутствием миграции фильтрующего материала и проскока задержанных частиц в результате скачка давления или другого внешнего фактора. Эффективность удержания таких фильтров обычно обозначают равной или больше 99% β1000, то есть β = 1000, а для наиболее критичных применений (защита мембраны стерилизующих картриджей, контрольная фильтрация пива) - 99,98% β1000, то есть β = 5000.
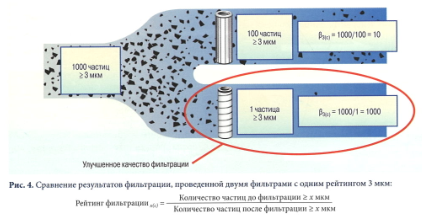
Сравнение результатов фильтрации с помощью пяти разных фильтров
Фильтр | Количество частиц до фильтра | Количество частиц после фильтра | Эффективность удержания, % | Коэффициент β |
---|---|---|---|---|
A | 5000 | 500 | 90 | 10 |
B | 5000 | 250 | 95 | 20 |
C | 5000 | 50 | 99 | 100 |
D | 5000 | 5 | 99,9 | 1000 |
E | 5000 | 1 | 1000 | 5000 |
Типы мембранных фильтров
Хочу напомнить, что понятия «номинальный» и «абсолютный» используются только для механических фильтров, но не для микробиологических. Принципиальная разница между механическими (глубинными) фильтрами для удаления частиц и мембранными (микробиологическими) заключается в следующем: глубинные фильтры характеризуются рейтингом, выраженным в микрометрах, и эффективностью удаления, выраженной в процентах или через значение β. Мембранные фильтры всегда имеют рейтинг меньше 1 мкм, но это вовсе не значит, что все фильтры рейтингом меньше 1 мкм могут называться микробиологическими. Микробиологические фильтры подразделяются на редуцирующие (сокращающие микробиологическую нагрузку) и стерилизующие.
Стерилизующие фильтры должны удовлетворять следующим требованиям:
- гарантировать отсутствие тестовых микроорганизмов (0 КОЕ) в фильтрате при нагрузке фильтра бактериальной суспензией с концентрацией 10 КОЕ на 1 см2 площади фильтра;
- должны иметь возможность проверки на целостность;
Фильтры, сокращающие микробиологическую нагрузку, должны удовлетворять следующим требованиям:
- обеспечивать определенное снижение бактериальной нагрузки на каждые 10 дюймов длины фильтра или на единицу площади фильтр-картона;
- позволять проводить тестирование на целостность;
- обеспечивать отсутствие микроорганизмов (0 КОЕ) в фильтрате (при этом проход клеток в количестве нескольких КОЕ является допустимым).
Показатель редукции титра Tr по смыслу аналогичен коэффициенту β для механических фильтров. Для нормальной и надежной работы стерилизующих картриджей необходима процедура систематического тестирования на целостность специальным прибором. Микробиологические фильтры вырабатывают свой гарантированный срок службы по достижении максимального количества циклов стерилизации. Производитель должен указывать предельное гарантированное суммарное время стерилизации при максимально допустимой температуре. Применение редуцирующих и стерилизующих фильтров требует систематических санитарных обработок. Обработка фильтра производится, как правило, в линии. Вода и дезинфицирующий раствор для санобработки должны быть предварительно отфильтрованы при рейтинге фильтрации не более 3 мкм абсолютных. Промывать и стерилизовать фильтр следует отдельно от общей системы во избежание засорения фильтров посторонними включениями.
Этапы фильтрации пива
Как выше уже говорилось, после грубой (кизельгуровой) фильтрации пиво поступает на последующие этапы фильтрации. Полный «каскад» фильтраций примерно выглядит следующим образом: трап-фильтрация (10 мкм) как защита от грубых загрязнений, тонкая фильтрация (5-1 мкм), финальная фильтрация и, возможно, стерильная фильтрация. Для стерильной фильтрации пива, как правило, используют микробиологические мембранные картриджи рейтингом 0,45 мкм. Но повторюсь, можно остановиться на кизельгуровой фильтрации и разлить пиво в кеги со сроком реализации около недели. Можно разливать и после любой другой ступени фильтрации, все зависит от желаемого результата. Используя различные по фильтрующему материалу и/или по удерживающей способности фильтры, мы можем с помощью одного и того же оборудования (фильтр-пресса, корпуса модульного или картриджного фильтра) проводить грубую, осветляющую, тонкую и даже обеспложивающую фильтрацию после подбора необходимого фильтр-картона, модуля или картриджа для получения желаемого результата. При этом следует обращать внимание на технические данные: максимальное рабочее давление, температуру, обработку поверхности, тип подсоединений и санитарное исполнение. Понимание целей применения тех или иных фильтров позволяет сделать правильный выбор при сравнении предложений от различных поставщиков.
Стабилизация пива
Сортовой особенностью некоторых типов пива, например нефильтрованного, дображивающего в бутылке, пшеничного и ряда других, является мутность. Но если мы пиво фильтруем, то оно должно оставаться прозрачным, с блеском, до конца срока годности - указанной даты на этикетке. И этот показатель качества может проверить любой потребитель пенного напитка без лабораторного оборудования. Пиво должно быть стабильным как по микробиологическим и физико-химическим (коллоидная стойкость) показателям, так и по вкусу и запаху (вкусовая стабильность). И в этой части статьи предлагаю вам рассмотреть холодный стерильный розлив как способ увеличения микробиологической стабильности пива. Для микробиологической стабилизации пиво обычно подвергают пастеризации. Существуют различные варианты пастеризации: пастеризация в потоке [пластинчатый пастеризатор (68-72 °C, 50-17 сек, ПЕ15)]; пастеризация в туннельном пастеризаторе; горячий розлив. Это очень надежные способы стабилизации пива. Но об этих высокотемпературных процессах мы говорить не будем, а напротив, рассмотрим холодную стерилизацию. Под этим способом подразумевают удаление микроорганизмов с помощью фильтрации. Ранее мы рассмотрели типы микробиологических фильтров. Именно с их помощью и осуществляется холодный стерильный розлив (рис. 5), который исключает негативное изменение вкуса пива в результате тепловой обработки. Для получения микробиологически стойкого пива недостаточно установить мембранные картриджи в цехе розлива, необходимо комплексно настроить весь производственный процесс и соблюдать главное правило пивоварения - обеспечение педантичной чистоты на всех участках производства.
Поэтому шаг первый - контроль санитарных условий на производстве. Под этим мы понимаем проверку соблюдения личной гигиены сотрудниками, чистоты санитарных инструментов (щеток, швабр) и мелких деталей (пробоотборников, уровнемеров и т. д.).
Шаг второй - безупречный микробиологический контроль на производстве (ступенчатый контроль, взятие и анализ особых проб в проблемных местах, ускоренная идентификация микроорганизмов, проверка смывов, отслеживание путей дополнительного обсеменения пива микроорганизмами из воды, воздуха, углекислоты, тары и т. д.).
Шаг третий - снова контроль санитарии, соблюдения графиков мойки и дезинфекции, контроль за температурой, концентрацией применяемых средств и временем обработки и как следствие - хорошее микробиологическое состояние трубопроводов, фильтров, С1Р-станции до зоны фильтрата и после.
Шаг четвертый - контроль соответствия условий работы аппаратов розлива и укупорки требованиям асептического розлива (с точки зрения мойки и дезинфекции, чистоты пробки и т. д.).
Шаг пятый - проверка состояния самих фильтров (соблюдения режимов работы и мойки, графика проведения тестов на целостность) и контроль режимов их эксплуатации (перепадов давления и т. д.).
И шаг шестой — это обеспечение стабильности самого пива, и для этого необходимо контролировать процесс, начиная с варочного цеха, с учетом используемого сырья, а также отслеживать концентрацию кислорода в пиве!
И вот если все это мы можем обеспечить, то можно рассматривать холодный стерильный розлив как альтернативу пастеризации.
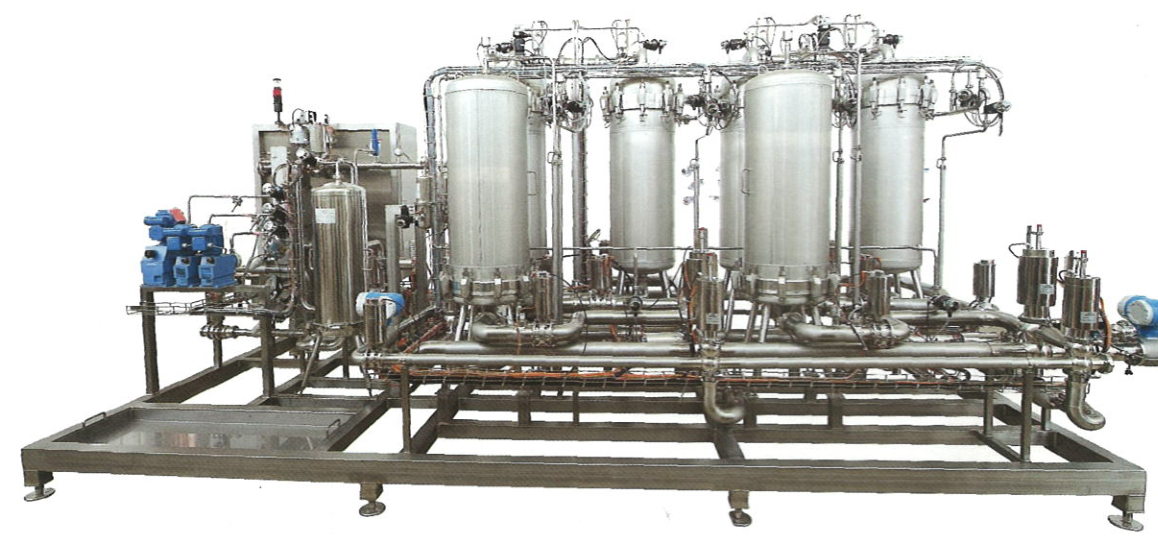
Коллоидная стойкость пива и стабилизаторы
Хочется заметить, что микробиологически стабильное пиво, даже пастеризованное, со временем мутнеет. И это помутнение вызвано коллоидно-растворенными веществами. Далее мой рассказ будет о коллоидной стойкости пива. Комплекс «полифенол - протеин» возникает вследствие образования водородного мостика между водородом фенольных гидрооксильных групп и кислородом пептидных групп. Эта сложная молекула совершает так называемое броуновское движение. Вследствие столкновения молекулы сцепляются друг с другом, укрупняются и возникает видимое помутнение (рис. 6). Этому способствует влияние следующих внешних факторов: температуры окружающей среды, взаимодействия напитка с кислородом и ионами металлов, перемешивания (встряхивания), света. Главным фактором, приводящим к образованию мути, является кислород, молекулы которого соединяются с молекулами как белков (пептидов), так и полифенолов в пиве. Ионы тяжелых металлов поддерживают процесс окисления и способствуют образованию осадка. При взбалтывании ускоряется процесс образования комплексов (белок + полифенол), а под действием света увеличивается окисление. И естественно, влияние температуры имеет огромное значение, так как с ее увеличением возрастает скорость химических реакций, то есть пастеризация также может быть толчком возникновения коллоидного помутнения. При понижении температуры образуется так называемое холодное помутнение. Этот прием используют в производстве, выдерживая пиво на дображивании при температуре около нуля (-2...0 °C). В результате понижения температуры образуются слабые водородные связи, которые разрушаются при ее повышении. Но при возникновении более сильных ковалентных связей образуется необратимая (постоянная) коллоидная муть. Если она появилась в ЦКТ (при холодной выдержке), то при наличии этапа последующей фильтрации мы ее удалим или она при долгой холодной выдержке останется в танке в виде образовавшегося осадка. Разобрав механизм возникновения коллоидного помутнения, можно сделать вывод, что оно вообще не произойдет, если мы частично или полностью удалим один из компонентов помутнения и воздействие вызывающих его факторов. Для этого существуют технологические приемы: применение ячменя с низ ким содержанием белка, менее 11%; использование мягкой воды; несильное выщелачивание дробины; корректировка pH готового горячего сусла (pH = 5,1...5,2); неранняя задача хмеля (полифенолы солода должны сначала прореагировать с белками); контроль за образованием взвесей горячего сусла; полное удаление горячего и оптимальное удаление холодного отстоя холодных взвесей; активное брожение и холодное дображивание; исключение контакта с воздухом и ионами тяжелых металлов. Все это поможет нам замедлить образование коллоидного помутнения, но не предотвратит его. Поэтому для получения физико-химически стойкого пива применяют стабилизаторы. Их использование не противоречит Закону о чистоте пива, если они удовлетворяют следующим требованиям: нерастворимость в пиве, отсутствие вкуса и запаха, химическая и биологическая чистота.
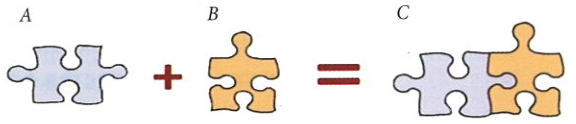
А - высокомолекулярный белок (полипептиды); В - высокомолекулярные полифенолы (таннины); С - комплекс (протеин - полифенол)
Для адсорбции белков используют силикагели, а полифенолы адсорбируют с помощью поливинилполипирролидона (ПВПП), как по отдельности, так и комплексно. Силикагели разделяются на гидрогели и ксерогели. Гидрогели содержат более 30% диоксида кремния, их влажность составляет более 50%, так как они не подвергаются заключительной сушке и за счет этого меньше пылят. В ксерогелях содержание диоксида кремния больше 80%. Эти продукты получены в результате реакции жидкого стекла с минеральными кислотами. Хочется отметить избирательность силикагелей, они адсорбируют только крупные цепи полипептидов и не затрагивают белковые соединения с меньшей молекулярной массой, которые участвуют в процессе ценообразования и пеностойкости. Важной характеристикой силикагелей является размер частиц, так как при маленьком размере будет быстрее забиваться фильтр и как следствие цикл фильтрации будет короче, а крупные частицы обычно менее эффективны. Лучшими адсорбционными свойствами обладают частицы размером от 8 до 20 мкм. Удельная поверхность силикагелей составляет 350-700 м2/г. Понятно, что чем она больше, тем лучше работает силикагель. Среднее вносимое количество для гидрогеля находится в пределах 50-100 г/гл, ксерогель дозируют в меньшем количестве.
ПВПП - органическое соединение, его протеиноподобная структура похожа на аминокислоту пролин, в результате ПВПП обладает способностью адсорбировать полифенольные (дубильные) вещества путем образования водородных связей, а водородная связь зависит от pH. При щелочном значении pH происходит десорбция фенолов, на этом основана регенерация ПВПП. Нерегенерируемый ПВПП применяется так же, как и силикагели, - задается в ЦКТ или на фильтрации через дозатор. Использование нерегенерируемого ПВПП является самым дорогим способом стабилизации, но современное оборудование для регенерации ПВПП доступно по цене даже для заводов небольшой мощности и может применяться в линии с любым типом намывных и мембранных фильтров. При содержании кислорода в пиве более 0,02 мг/л использование ПВПП не рекомендуется, поскольку возможны проблемы с вкусовой стабильностью этого напитка.
Еще один продукт - силиказоль - коллоидный водный раствор кремниевой кислоты, частички которой не имеют никаких пор, но несут электрический заряд. Благодаря заряду частички силиказоля связываются с белковыми соединениями с образованием гидрогеля, который оседает в виде плотного осадка. Таким образом, силиказоль хорошо осветляет пиво и улучшает его фильтруемость, но в меньшей степени используется для повышения коллоидной стойкости пива. Так, если стоит задача получить относительно прозрачное пиво (мутность 1-2 ед. ЕВС) без фильтрации и сепарации, то дозировку подбирают из расчета 200-400 мл/гл пива и время контакта в течение 3-5 дней. Если же силиказоль применяют для улучшения фильтрации, то дозировку и время контакта уменьшают - соответственно до 100-200 мг/гл и 1-3 дней. При использовании холодного охмеления силиказоль добавляют не раньше, чем через сутки после охмеления.
Тщательный анализ всех аспектов стоимости фильтрации и стабилизации с учетом индивидуальных особенностей производства незаменим для снижения затрат на единицу объема фильтруемого пива. Правильно подобранные решения позволяют минимизировать издержки производства без ущерба для качества пива.